Extrusion control
(AWT / PWT / SFDR)
Extrusion control is a part of the process
control document starting from the version 2.35. The extrusion control
is used to store the description of the extrusion process in case the
simulation of the parison extrusion is required.
The parison thickness profile during extrusion can be
controlled by Axial Wall Thickness control
(AWT), Partial Wall Thickness control (PWT), and Static
Flexible Deformable Ring control (SFDR).
To include the extrusion simulation, check Include
extrusion control at the top of the process control window. Now,
to edit the extrusion settings, click on the toolbar button "Extrusion
control" on the left side of the process control window.
AWT / PWT control data
The following window is displayed after click on "Extrusion
control" button. In this window, AWT/PWT control data are displayed.
To display and edit SFDR data, click on the tab
"SFDR" on the right top side of the window.
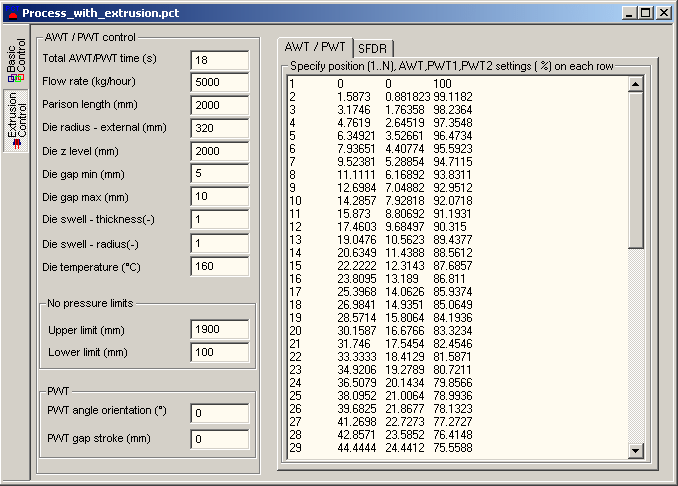
Fill in the extrusion control window with appropriate
data:
Total time - Specify the total time used during
the extrusion simulation. The time is divided into N steps (where N
is number of rows, i.e. control points, in AWT / PWT control box). The
extrusion process always takes the time specified as Total time. The
molding process is delayed until the parison is extruded, i.e. the molding
process (as described in the basic process control),
starts immediately when the parison extrusion finishes.
Flow rate - flow rate from the extrusion die during
the extrusion process
Parison length - how long the extruded parison should be (a guess).
This values is used for parison scaling before the simulation starts.
This means the parison from *.bcs file is scaled to have the length
specified.
Die radius - external - external radius of the extrusion die
Die z level - position of the extrusion die outlet
Die gap max, min - maximum and minimum thickness achieved with
AWT, corresponding to 0% (min. gap) and 100% (max. gap) of AWT setting,
when both PWT controls are set to 50 %.
Die swell thickness, die swell radius - swell ratio (1 means
no swell) of thickness and radius
Die temperature - temperature at the die outlet
No pressure limits - where the pressure should not inflate the
parison (upper and lower limit of z coordinate). The parison is inflated
only between<lower limit, upper limit>
PWT - values connected particularly with Partial Wall Thickness
control:
PWT angle orientation - Orientation of
the PWT control in the X-Y plane (rotation around z axis). This orientation
angle is used also for SFDR control. For details
see AWT and PWT control specification.
PWT gap stroke - PWT control value (between 0 and 100 %) is converted
to a real value influencing the extruded parison thickness. The gap
stroke corresponds to the full range of the PWT control. The interval
<0%, 100%> corresponds to < - gapstroke/2, +gapstroke/2>.
AWT / PWT control settings
In this box, specify AWT (PWT) control position (1 .. N, N is typically
64), AWT setting (%), PWT1 setting (%) and PWT2 setting (%) on each
row. Some typical settings are below:
1 100 50 50
2 100 50 50
3 100 50 50
4 100 50 50
...
60 100 50 50
61 100 50 50
62 100 50 50
63 100 50 50
64 100 50 50
|
In this case, 64 control positions is used, where AWT is everywhere
100% (the extrusion die is open at maximum gap). PWT1 and PWT2
is everywhere 50% (this means that PWT does not influence the
extruded parison thickness at all). The extruded parison will
have constant thickness, specified in Die gap max box.
|
More details about AWT and PWT can be found in the AWT
and PWT control specification.
SFDR data
SFDR control data can be specified using the SFDR sheet
- just click on SFDR tab to display it:
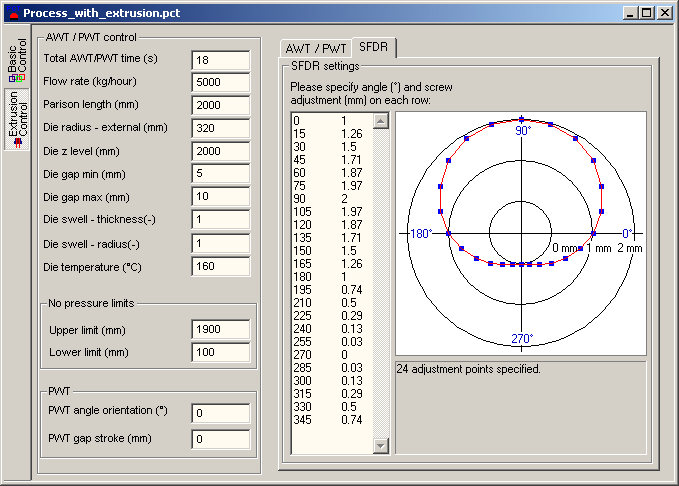
To describe SFRD control:
- Specify on each row an angle in the range <0°, 360°),
where an adjusting screw is located and the screw adjustment in the
range <0.0, 2.0> mm.
- Make sure that the data starts with the angle 0°.
- Do not specify the adjustment for the final angle (360°), as
this adjustment is supposed to be identical with the one specified
for 0°.
- It is possible to specify whatever number of adjusting screws,
B-SIM automatically scans the data and estimates the number. However,
a typical extrusion equipment uses 12 adjusting screws.
More details about SFDR can be found in the SFDR
control specification.
Important:
The extrusion process itself, when included into a simulation, delays
the molding process until the required "Total time" is reached.
You can specify the basic process control as starting at time 0 ms,
and B-SIM will automatically add a time shift obtained due to the extrusion
process.
Once all the necessary data are specified, use File /
Save or File / Save as command to store the extrusion and process control
data, or switch back to the basic process control
(just click on PCT button on the left toolbar) to continue with
the process control editing.
Back to top of this document